Jos Balendonck (left) and Jochen Hemming with ‘their’ Sweeper.Text Roelof Kleis photos Sweeper EU and Guy Ackermans
Sweeper is the youngest harvesting robot in the Wageningen agro robotics family. It resides in Phenomea, the demonstration facility next to Axis. When it is standing still it is a clumsy-looking piece of machinery. Not much more than a large, narrow, yellow chamber on wheels with a robotic arm attached to the carrier. But just wait until it comes to life. You can see it best in the promotion video made in the greenhouse at De Tuindershoek sweet pepper farm in IJsselmuiden. The YouTube film (also on sweeper-robot.eu) is the Plant Sciences Group’s blockbuster of the year, says Jochen Hemming of Wageningen Plant Research (Greenhouse Horticulture). It’s been seen 25,000 times in just a few months.
Watch the sweeper at work:
What the film shows is this: the Sweeper robot moves down the rows of sweet peppers, stops by a pepper, scans the surroundings, approaches the vegetable from the appropriate side, cuts through its stalk, catches it in its hand and puts it in a crate. It takes an average of 24 seconds to do all this. A world record, if you compare it with its predecessor, Crops. Three years ago, this first-generation sweet pepper harvesting robot, another WUR creation, took 90 seconds to get a pepper into the crate. That won’t get the harvest in on time.
Six seconds
But the same goes for Sweeper, a joint project by WUR and Swedish, Israeli and Belgian colleagues. The robot may be four times faster than its predecessor, but it still can’t keep up with a human being. We can pick a pepper in about six seconds. And we pick all the peppers, not just those hanging within easy reach. The Sweeper cannot do that yet.
‘The robot only sees some of what’s visible,’ explains Hemming. ‘It doesn’t notice clusters of peppers. Sometimes there are leaves in the way. And peppers on the inside of the plant are not very accessible. In fact, it can only harvest the peppers hanging on the outside.’ So in today’s commercial greenhouses, Sweeper will only manage to harvest 55 per cent of the ripe peppers, and only after they have been ‘declustered’ and some foliage has been cleared that is in its way. Even that is an improvement though: Crops only spotted one in three ripe peppers.
Viable
Project leader Jos Balendonck of Wageningen Plant Research (Greenhouse Horticulture) nevertheless sees some future in a commercial application of the robot. ‘The growers want a robot that scores 100 per cent because there is such a shortage of labour. We don’t achieve that with the Sweeper yet in today’s growing systems. But I think that we have a good business case even with a robot that gets in half the harvest. People can do the other half, and that option could be viable too. As long as the robot speeds up. Preferably to the same speed as a person. All the stages in the process need to get faster. I think we’ll manage that within three to five years. We’d like to do that in a follow-up project.’
In the longer term, over five to ten years, it should also be possible to create a robot that can pick the entire harvest, thinks Balendonck. But that will require more than just an improved Sweeper. ‘Then the cultivating system needs to change too. The plants are now grown up wires hung in a V shape. So they are double rows and the Sweeper can only access one side of the V. You’ll have to switch to a system with single rows of plants. Breeders can also develop varieties that work better for a harvesting robot. Plants with fewer clusters and less foliage to get in the way.’
Gripper with eyes
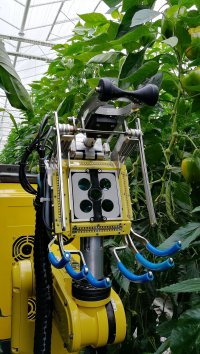
Sweeper has a long robotic arm with a combination of a head and a hand. Its visual system is in the head, where two cameras in the central eye make colour and depth images. Four infrared lamps around the central eye give the light needed for the depth image. Rows of bright LED lamps around the edge of the head provide uniform flash lighting for the colour image. This way the camera creates 20 images per second. The sweet pepper is viewed from several sides to give Sweeper a good impression of the surroundings. This detection system was developed by Ruud Barth, who recently got his PhD with distinction. The head/hand then approaches the pepper and a fast-moving knife cuts it off. The Sweeper’s blue ‘fingers’ capture the fruit and deposit it in a crate. The robot has been tested on yellow peppers but it can work just as well on other colours.
FlexCRAFT: self-learning robots
Robots are good at endlessly doing the same things in the same way. They cannot deal with variation. According to Professor Eldert van Henten of the Farm Technology Group, this is an obstacle to developing robots for agricultural purposes. After all, there is a lot of variety in nature. This problem is going to be addressed by the new FlexCRAFT programme, a joint venture of the four technical universities, including Wageningen, that form 4TU, the University of Amsterdam and businesses. The aim is to find a way to teach robots basic skills that they can use to carry out new tasks. In four years’ time, that should produce new applications such as a better Sweeper that can pick tomatoes as well as peppers. Or a robot for packing fillets of chicken or sweets. WUR is leading the four-million-euro project. In his group, Van Henten can employ two PhD students and two postdocs to work on it.